
Plasters can be mechanically mixed through both batch and continuous processes. Mechanically mixed plasters develop uniform casts with optimal strengths. Hardness, and other important properties. Mixing Mixing the plaster slurry is one of the most important steps in producing plaster casts with maximum strength, See bulletin IG503 for specific soaking instructions. Small batches require less soaking than large batches. The plaster should be fully dispersed in the water prior to mixing. Do not drop handfuls of plaster directly into the water. Soaking Sift or strew the plaster into water slowly and evenly. The water-to-plaster ratio is critical because it governs the strength
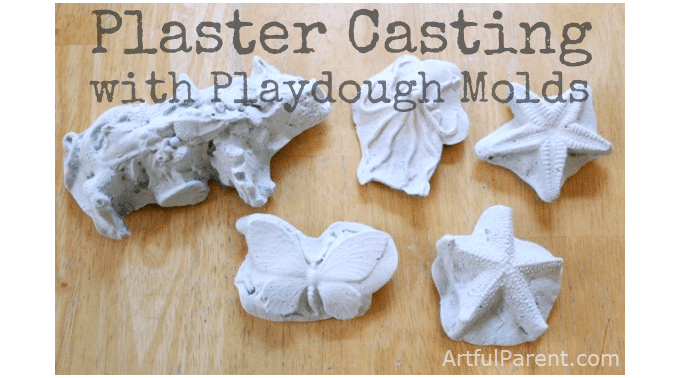
Measuring Weigh both the casting plaster and water for each mix. The higher the temperature of the water, the shorter the set time. Since variations in slurry (the casting plaster and water mixture) temperature produce variations in setting time, it is important to keep both the plaster and water in a stable temperature environment prior to use. Preparing the Mix Use potable water at temperatures between 70 and 100 ☏ (21 and 38 ☌). Compressive Strength 1,200 psi 8.27 MN/m2ĭry Compressive Strength 2,400 psi 16.55 MN/m2 Use Consistency (parts of water by weight per 100 parts casting plaster) 65 65ġ Hr.

#1 CASTING PLASTER is similar to white art plaster, except mixed at a lower use consistency to increase strength, chip-resistant, and to further minimize paint absorption. Hard working surface with reduced paint absorption. Industry standard for figurines, plaques and lamp bases.
